Would you believe us if we told you that we typically achieve less than 2% construction cost premium on our net zero buildings, compared to ‘business as usual’? Sounds too good to be true, right?
The key to achieving net zero at negligible construction cost premium is to approach the design as an integrated system. We use strategies such as enhanced envelope performance, better ventilation heat recovery, and supplemental heating and cooling at the zone to reduce the cost and size of mechanical infrastructure. When the mechanical system and space savings is taken into account, there is typically enough savings to offset the additional cost of investments such as triple glazing and geothermal bore fields.
Renewable energy at the scale to offset 100% of the energy for a building can be expensive, but our clients often rely on a power purchase agreement (PPA) to procure renewable energy. A PPA is where a third-party installs, manages and maintains a renewable energy system and sells the energy to the building owner. This means that the building owner does not have to cover the cost of installation, and they typically pay less for the energy than they would have paid the utility company. It’s a win-win.
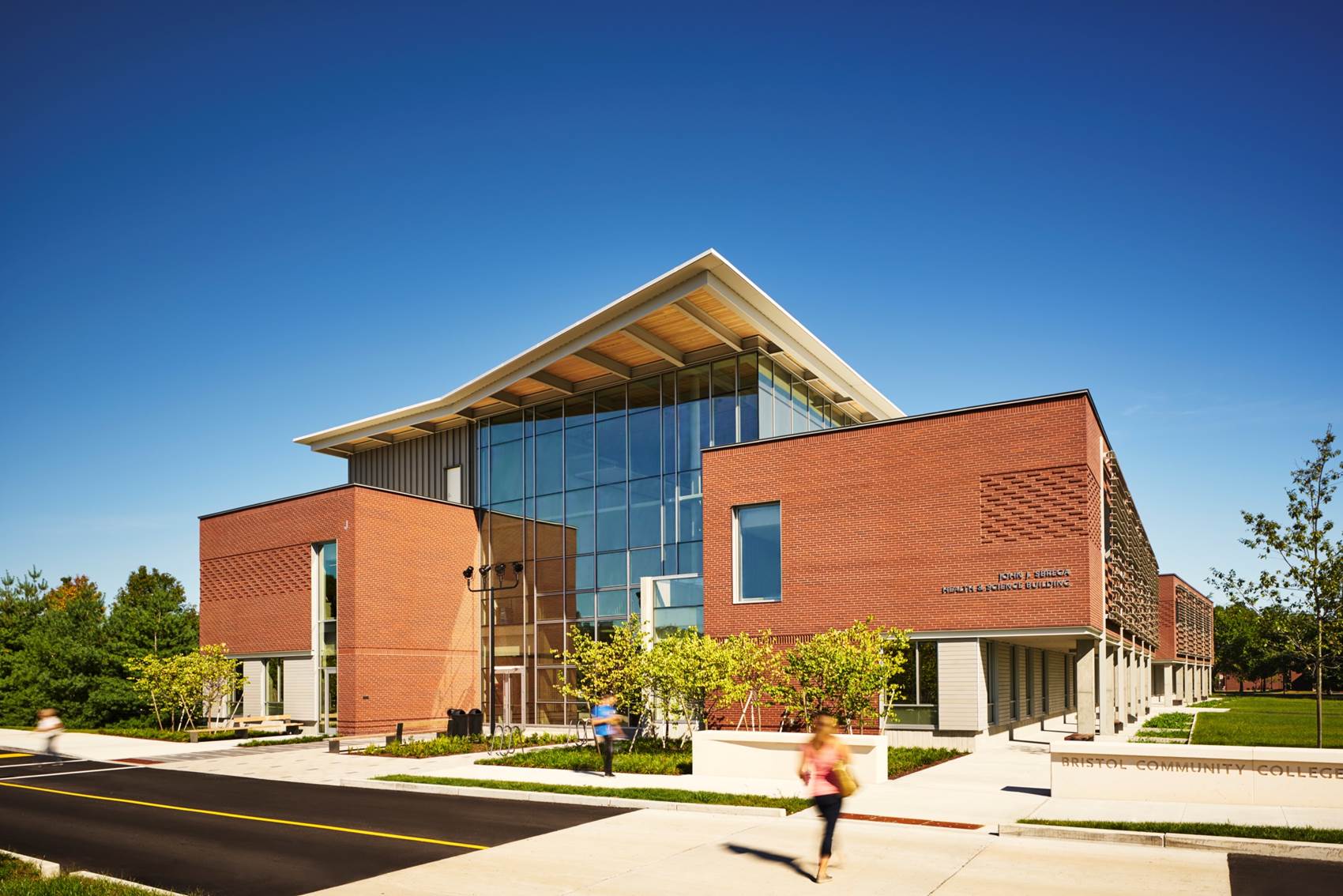
Image provided by Sasaki
The Sbrega building at Bristol Community College is an example from BR+A’s portfolio that achieved net zero at only 1% construction cost premium. How do we know? Because, it began as a typical ‘high performance’ design, achieving only 20% energy savings below ASHRAE 90.1-2007 (the energy code baseline at the time). Before the net zero energy goal was even considered, the project had already received approval and funding from the state and could not seek additional funds.
When the client asked us to help them achieve their climate action plan, we developed a new design to achieve net zero (Class B Site, Source, Carbon), in parallel with the ‘high performance’ design. Ultimately, the construction cost premium for the net zero design was only 1% of the construction budget. This minor uptick was easily absorbed by the construction escalation value carried in the original cost estimate.
The chart below shows the items that were reduced to decrease construction cost “SAVINGS” that essentially paid for the items that increased construction cost “COSTS”. In operation, the building and the PPA result in operating savings “REVENUE +” of $230,000 per year. That is equivalent to the tuition for 50 students per year. Net Zero is a true triple bottom line solution with environmental, financial and social benefits.
It is the first verified zero net energy laboratory in the US. You can read more about this award-winning ZNE building here.
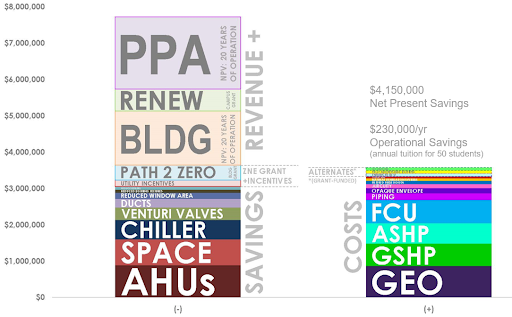
Another example is the 250,000 SF Chelsea Soldiers’ Home, an ASHRAE-170 inpatient healthcare facility that provides housing and care for veterans. Different from Bristol Community College, this building began with the objective of minimizing fossil fuels and being net zero ‘ready’ (capable of achieving Class D Site, Source, Carbon).
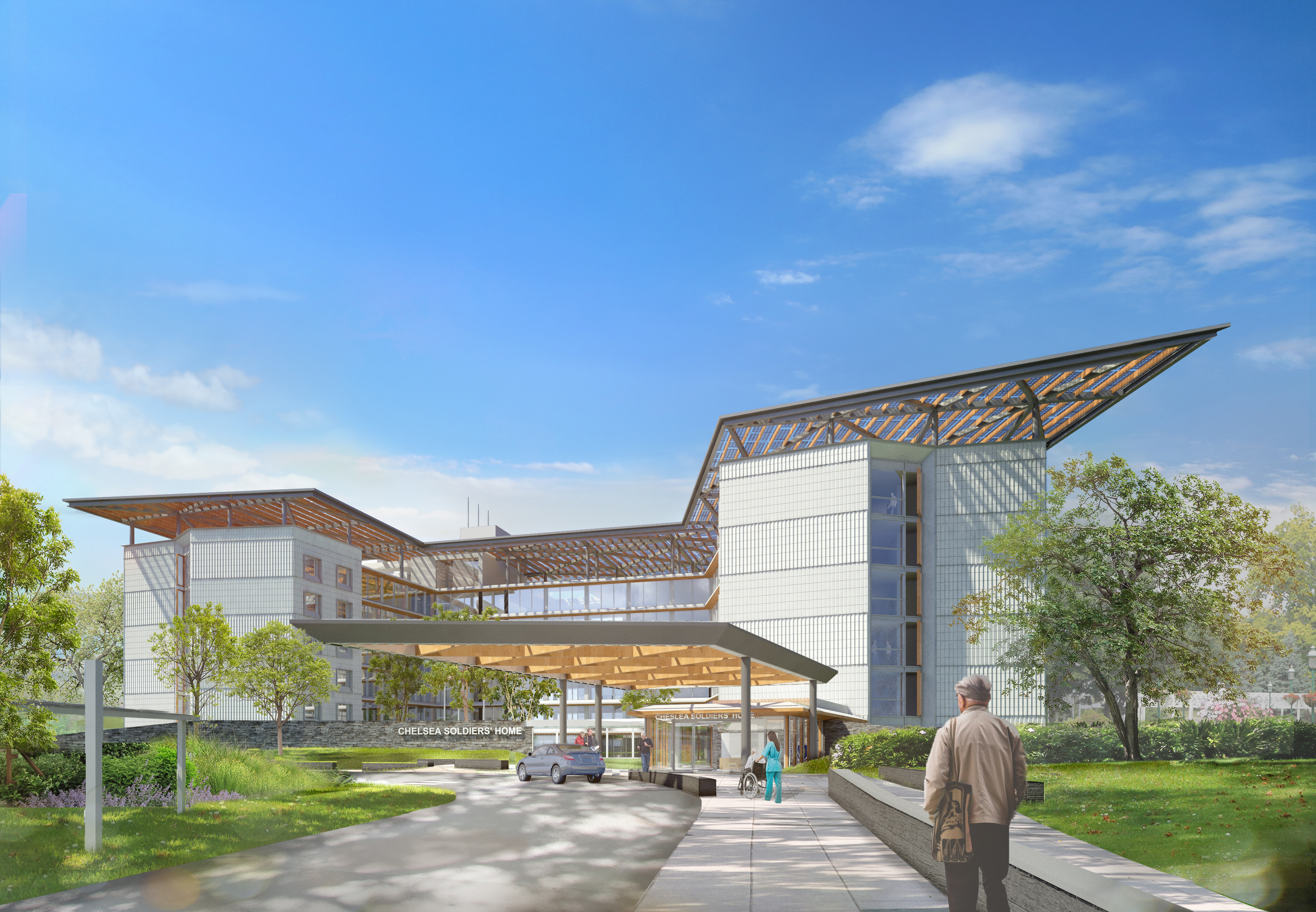
Image provided by Payette
The building relies 145 closed loop U-bend bore holes, installed to a depth of 500 feet each. Connected to the bore field are heat pump dual-wheel DOAS air handling units for ventilation air and water-source variable refrigerant flow systems with ducted fan coil units for zone conditioning. Water-source heat pump chillers with thermal storage generate domestic hot water. Due to its healthcare function, gas-fired boilers are installed to provide back-up heating only. The envelope is super-insulated and has triple glazing. A 0.5 MW solar array floats above the roof on a steel structure. The building is a pilot project for the utility incentive program, taking a holistic approach to maximize incentives for net zero buildings. To complete the utility incentive study, it was necessary to develop a detailed ‘business as usual’ minimally code compliant baseline design. A detailed construction cost estimate was provided by the construction manager for this code baseline option, for comparison to the final CD-phase construction cost estimate.
The cost analysis showed that the net zero design carried a premium of only a fraction of a percent of construction cost. How is this possible? The conventional baseline relied on an all-air VAV with reheat system, a large water-cooled chiller plant, perimeter heat, and other typical features. These systems are not only large and expensive, but they also require more shaft space and greater floor-to-floor height.
To learn more about the cost of net zero energy buildings, you can read this report: USGBC MA Zero Energy Buildings in Massachusetts: Saving Money from the Start. BR+A was a contributor and reviewer of the report. A few BR+A examples are included.